SETTING THE STANDARD
Colin Ross and Jo Pomeroy are the type of pastoralists and leaders all industries seek. Ross defines himself by his actions and nothing else.
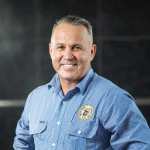

Colin Ross and Jo Pomeroy are the type of pastoralists and leaders all industries seek. Ross defines himself by his actions and nothing else.
On the sprawling properties of Limbunya and Maryfield Stations, in vastly different landscapes, Colin and partner Jo are setting standards they hope others will follow and at the same time creating a scalable, high performing cattle business in the Territory.
For more than 15 years North Star Pastoral has been producing quality export cattle to supply the Asian markets. The jewels in its Territory crown are Maryfield Station, located 100 kilometres south-east of Katherine and Limbunya Station which is in the Victoria River Downs district near the Western Australian border.
The properties cover more than 660,000 hectares and carry 60,000 head of Brahman and Brahman-cross cattle. Brahman Cattle are a Bos Indicus breed (originated in India) that are well suited to the conditions of the Northern Territory for a multitude of reasons.
They are highly adaptable; their thick skin helps their resistance to parasites, their glossy, sleek hair reflects much of the sun’s rays, and their additional loose-fitting skin assists them in the hotter months as they sweat through their pores much like humans.
Maryfield Station has a newly built 10,000-head capacity feedlot — one of only a handful in the NT — and all weather bitumen road access, a rarity for many NT stations. This export and abattoir preparation facility allows the fattening and finishing of cattle to accurate weight ranges to supply a wide range of export and domestic processing markets, all year round.
And judging by what they have built so far, it shows what is possible when there is a determined focus. “When we set about building the feedlot finishing facility, we wanted there to be three standards,” Ross outlines while driving the buggy around his yards. “It had to be about exceptional animal welfare, labour efficiency and outstanding occupational health and safety.
“And I think we have delivered that.” The constructed feedlot we drive through holds 5,000 head of cattle, while across the way a second feedlot holding the same amount is being completed. The cattle are slowly making their way to the feed after the specialised feed mixer and distribution unit delivers a regulated mixture of molasses, soy meal and hay to the cattle at optimised intervals.
“I went around the world looking at what others did and the most efficient feedlots didn’t have troughs. This met two important criteria of the three I set out – it was better for animal welfare because they couldn’t knock the troughs over, stumble and hurt themselves and it meant I didn’t need the staff to clean them down,” Ross said.
Ross will soon add a robotic sweeper to the covered feedlot to sweep up the mixture to minimise waste – again saving labour.
Further around we pass the double width dip which lessens the stress on beasts. It means a flighty beast can do a full 360 degree turn to find its way out. Meanwhile over at the loading pens he has built a curved roof to ensure that staff processing cattle and the cattle are protected from the sun.
Managing the construction and design of Ross’s overall vision is Cameron Mackie from Argyle Engineering. “Colin gets things done,” Mackie says as the simplest assessment to what has been constructed.
“He told me to build it like I would if I owned it. He was very clear on the three key principles he wanted maintained. I told him a curved roof wasn’t needed, it was going to be more costly and technically difficult, but he told me to do it anyway because it was the best solution.”
At the back of the property is a manmade dam which is filling with wet season rain. The water filled hole has been dubbed “Lake Colin”. It will be the source of a gravity-fed water system for the feedlot. From the top of the 15m mound which has been built you can see the silos which house the feed and the mixers for the cattle.
In the buggy again, Ross takes us through his trucking maintenance shed. The shed is a little over 100m long and has a full length pit to make it easier to service the fleet of trucks that “North Star Heavy Haulage” operates.
North Star Heavy Haulage managed by Jo, has a fleet of nine modern Kenworth Prime Movers all with 6 full deck crate units, which further complements North Star Pastorals cattle operations and enables the efficient movement of cattle between properties, as well as to sale or export.
In addition to managing North Star Heave Haulage, Jo also drives her Kenworth road train “Daisy Duke”. The trucks also cart fodder, supplements and other freight and machinery between North Stars Properties and from supplier to property. Based out of the Head
Office Facility in McMinns Lagoon (Darwin Rural), in addition to carting North Star’s cattle, the trucks are also contracted out to cart cattle for other producers around Australia.
The sheer industrial scale of the shed and the trucking component has to be seen to be appreciated. The determination to make it an easy place to live and work is also appreciated.
A formidable team, Colin and Jo have set out to make the property as sustainable as possible. They have combined the small and the large to make the property further self-sufficient. They both invested heavily in renewable energy with solar and battery storage and now only run the generators for an hour in the morning and an hour in the afternoon.
They use the roof of the staff undercover car parking to erect the solar panels. They also went to the trouble of investing in water efficient toilets. The cistern fills with the excess water you use to wash your hands.
To Colin and Jo every little bit helps, and they are doing everything to ensure the little things make properties more sustainable and efficient.
Late last year, the power couple put the properties on the market. They are expected to fetch more than $150 million. Agents, Danny Thomas and Olivia Thompson said it is the right time to sell the properties.
“To really maximise the benefits of what has been developed on Maryfield, it needs people with greater resources that can add cash and cattle and take it to the next level,” Thomas said.
“Colin and Jo are keen for someone else to take on the stewardship of the asset from here. Maryfield and Limbunya are the industrial portion of North Star Pastoral’s portfolio and they tie beautifully together.”
Colin Ross himself says he hasn’t built a property; he’s built a business. A business which can service the live export destinations of Indonesia and Vietnam, as well as the southern domestic processing markets.