OUR UNIVERSITY LEADS BY EXAMPLE
Charles Darwin University has responded to the Covid-19 pandemic in the most practical and innovative way – by designing face shields that can be manufactured in the Northern Territory.
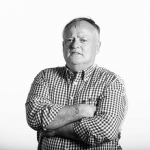

About 1000 of the shields are to be delivered to Royal Darwin Hospital. The university’s initiative is another demonstration of how Territorians have, in many ways, set not just a national but global example of how to respond to the coronavirus crisis.
Only a few cases of Covid-19 were diagnosed in the Territory; there was no community transmission and, mercifully, not a single death. The Advanced Manufacturing Alliance – a university research, trades and industry group originally put together to explore another Territory innovation, the SPEE3D metal printer – worked to develop designs that could be produced locally.
AMA Director Dr Rebecca Murray says: “Covid-19 has had an unprecedented impact on communities around the world. “Basic equipment and supplies are being strained, and this has provided us an opportunity to help out where we can.” The AMA gathered ideas from the community and sought advice from the Territory medical community on how best to help. “We came up with two face shield designs that have been trialled by doctors and nurses at the Royal Darwin Hospital,” Dr Murray says.
The shield used commonly available optimised A4-size transparencies for the face protection with a crescent shaped visor water-jet cut by Darwin Profile Cutting from solid polymer sheet to provide added protection from overhead droplets. “The sheet polymer used is known for its low porosity, heat resistance and ability to be sterilised effectively.”
CDU engineer Matthew Harbidge says an important consideration while ensuring the equipment suited the needs of health workers was ease of manufacturing and scalability. “One of the aims of the project was to provide a Therapeutic Goods Administration-registered design that we could provide for others around the world free of charge,” he says. “The visor design has a manufacturing time of one minute.
It can be manufactured locally by anyone with an appropriate 2D laser or waterjet cutter. The design is also suitable for 3D printing, so has excellent potential for scalability or custom just-in-time manufacturing.” Royal Darwin Hospital director of ICU Dr Paul Goldrick says due to global supply chain problems it was reassuring to know a locally manufactured option for a critical item such as a face shield was available for Territory health care workers.
Australian Army soldiers were involved in design discussions and helped in the production of the face shields. The soldiers also printed 25 face shields and distributed them to police control points around the Territory for potential use by ADF personnel in support of the NT Government response to Covid-19.
The AMA has shared the designs on its website under a Creative Commons Licence. For more information visit: advancedmanufacturing.cdu.edu.au/ designs TQ