FULL SPEED AHEAD
Steve Camilleri’s life dramatically changed for the better when he was put in a class for gifted children at school. Suddenly, the 10-year-old socially awkward boy was surrounded by like-minded fellow students.
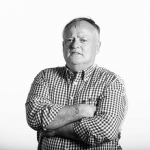

“Life had been hard up until then,” he says. “I didn’t have any friends and my parents were tearing their hair out about what to do with me. “Other kids were playing football, but all I wanted to do was carry out modifications to the motherboard on the school’s computer.” Steve went onto pass Year 12 electronics when he was in Year 7 at Parap Primary School in Darwin – with a 100 percent mark.
He was invited to meet the Administrator at Government House with other Northern Territory students who had gained perfect scores in their subjects. “There was little 11-year-old me with all these much older kids towering over me.” It was all a sign of things to come – an incredibly bright Territorian driven to solve technical challenges, to invent, to innovate, to do things differently. “There’s more to my drive than a simple desire; I have to do it,” he says. “It’s like a boy who discovers at the age of 12 that he can kick a ball straight through the posts from halfway down the oval. He has to be a footballer. He doesn’t really have any choice.” Steve is now an entrepreneur and recognised as a world-class design engineer. He and business partner Byron Kennedy have invented a 3D metal printer that works up to 1000 times faster and up to 100 times cheaper than any other printer.
A metal foundry in Western Australia took eight weeks to make a fastener known as a clevis; LightSPEE3D did it in an hour at a tenth of the cost. The printers are being sold to a range of industries. Steve says it will be up to private enterprise to decide exactly how the printers are used. “The printers can be used to manufacture a vast range of products, such as car and machinery parts. They can do the job faster, cheaper and more efficiently than any other 3D printer in the world. And they are easy to use. “We have developed the printer to revolutionise manufacturing – the applications are almost limitless.” Conventional 3D metal printers work by using lasers to melt powdered metal one layer at a time. LightSPEE3D uses a rocket engine to propel metal powder at three times the speed of sound so that it instantly bonds as the new object is built up. “There’s no waiting time for the metal powder to melt and cool,” says Steve. The printer has no pretensions – other printers can make more finely detailed parts; LightSPEE3D produces the kind of parts usually made in a foundry.
Life may have been very different if teachers at Parap Primary hadn’t recognised his high intelligence and put him into the school’s Gifted Unit. Steve never boasts about his brainpower – but he is a strong advocate of highly intelligent students being guided into gifted classes, or at least being put together with like-minded children, not only because they are probably the great inventors and big thinkers of the future but because they are often extremely emotionally vulnerable. The suicide rate among those with exceptionally high IQs is much higher than the national average.
“I didn’t fit in with most of the kids at school,” he says. “But I was happy immediately I was put into the Gifted Unit.
We fed off each other – sharing ideas, discussing challenges. I had other kids to talk to about the things that interested me. “It was marvellous.” Steve, who was born in Canberra but moved to the Top End at the age of six, went onto Darwin High School after Parap and then gained an engineering degree and then Masters at Charles Darwin University. There are two versions of the printer: Light SPEE3D, which makes metal parts weighing up to 5 kilograms, and Warp SPEE3D, which manufactures much larger parts, such as gear box housing and fan wheels, up to 40 kilograms.
“The claims we have made for our 3D printers are very big,” says Steve. “And big claims demand a lot of proof. “So we have spent a great deal of time and effort testing our technology to prove that it works.” The world is beginning to get the message. Last September, Light SPEE3D was named the world’s best 3D printer at the TCP “academy awards” in London. “It’s the highest award in the industry,” says Steve. “We didn’t expect to win so sent an investor along to the awards night – he had to make up an acceptance speech on the spot.” A $2.2 billion American company, Desktop Metal, came second.
“We are very pleased that a little Darwin company took on the big boys and won.” Steve and Byron took another giant step forward earlier this year when they sold a Warp SPEE3D machine to Carl Fruth’s German company FIT. “This has given our work enormous prestige. Carl is considered the industry soothsayer – everyone in the business wants to know what he’s doing.” The printers represent an extraordinary step forward in manufacturing. He was part of the university team that developed the Desert Rose, which won the Darwin-to-Adelaide World Solar Challenge in 1996 and held a world solar car speed record for many years. “We were consistently in the top 10 in the race, but our car had one of the lowest budgets. We built everything in Darwin.”
Steve and Byron set up a company called In Motion Technologies, which developed a new motor drive system. The duo designed the electric bike for Avanti, solar aircraft motors for NASA and a hybrid mower for John Deere. They were bought out by a big American company but stayed on as research and development managers. Several years of frustration followed. “We found that manufacturing was hampering innovation because commercialising a product required enormous capital expenditure. A lot of the things we were inventing just didn’t make it to production.” The two men decided to go it alone and began working on a super-fast 3D printer, promptly winning a prestigious Bosch engineering award. Steve and Byron, who have received generous help and support from the Federal and Territory governments, the Darwin Innovation Hub and Charles Darwin University, recognise that the tyranny of distance makes commercialising an innovative product from Australia extremely difficult.
“The way the rest of Australia looks at the Territory is the way the rest of the world looks at Australia. “We are severely handicapped when it comes to getting our invention to market.” Steve spends a great deal of time flying overseas, mainly to the three key markets, the United States, Germany and Japan. He is looking forward to a vigorous sales campaign. “We’ve got the technology, we know it works, we know it makes commercial sense.” Steve met his wife Christina while they were both studying engineering at Charles Darwin. They have three daughters: Natalie, 11, Emily, 8, and five-year-old Lily. “You won’t be surprised to hear that they’re all techy kids.” Steve is pleased that the world’s attitude towards clever people is changing. “It’s almost trendy to be a nerd nowadays. People used to say, ‘Urrgh! You’re a geek!’ Now it’s, ‘Oh, you’re a geek’. “I hope that never changes.” TQ